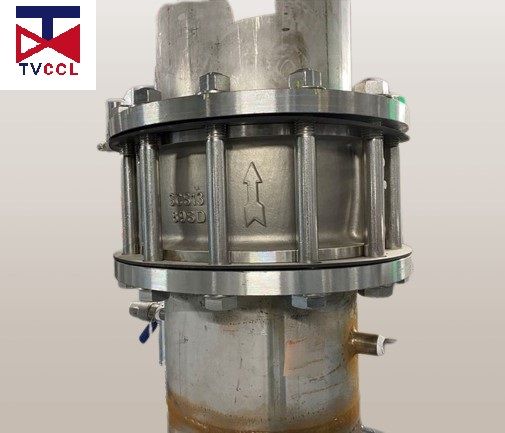
Q:Why need installation distance 6 to 8 pipe diameter is perfect for dual plate check valve?
The optimal installation distance of 6 to 8 pipe diameters for components such as check valves in piping systems is based on fluid dynamics and flow behavior within pipes. This distance is considered ideal. TVCCL will explain the reasons as follows
Flow Stabilization: When fluid exits a pump, passes through a bend, or flows past other obstacles, it can become turbulent. Turbulent flow is chaotic and can prevent valves and other components from working properly. The flow needs some distance to pass from turbulent to laminar (smooth, streamlined). Typically, a distance of 6 to 8 pipe diameters allows the flow profile to stabilise and become more uniform.
Reduction of Turbulence: Turbulence can lead to increased wear on valve components, reduced efficiency and potential cavitation (formation and collapse of vapour bubbles). Allowing sufficient distance for the flow to become laminar can minimise these problems.
Prevention of Water Hammer: Water hammer is a sudden surge of pressure caused when a moving fluid is forced to stop or change direction suddenly. When a check valve closes rapidly due to turbulent flow, it can cause water hammer. A more laminar flow profile allows the valve to close more smoothly, reducing the risk.
Accurate Instrument Readings: For flow meters or other instruments to give accurate readings, they require a stable and uniform flow profile. Disturbances can lead to erroneous readings. A distance of 5 to 10 pipe diameters ensures that the flow is stable until it reaches these instruments.
Optimal Valve Performance: For a valve to perform at its best, it must operate in the conditions for which it was designed. A stable flow profile ensures that the valve can open and close as intended, ensuring optimum performance and longevity.
Safety: Stable flow reduces the risk of cavitation, water hammer and other phenomena that can damage piping and compromise safety.
Energy Efficiency: Turbulent flow has higher energy losses due to friction and drag than laminar flow. By ensuring a laminar flow profile, the system can operate more efficiently, resulting in energy savings.
In summary, the recommendation of 6 to 8 pipe diameters as an installation distance is based on the principles of fluid dynamics and the need for a stable, laminar flow profile for optimum system performance, safety and efficiency.
This is a general guideline, specific applications and system designs may require adjustments.
- Related Products
Dual Plate Wafer Type Check Valve
TC0
Fast Delivery: Most orders are shipped within 3-7 days, depending on stock availability. Versatile...
DetailsDual Plate Wafer Type Check Valve with Full Rubber
TC1
Dual plate wafer type check valve with full rubber is usually used in seawater desalination...
DetailsDual Plate Wafer Type Check Valve With Retainerless
TC8
The dual disc check valve with its compact wafer design and low cost have made it a popular...
DetailsDual Plate Lug Type Check Valve
TC6
The dual plate lug type check valve only takes 15-20 minute completely dissemble and reassemble...
DetailsDual Plate Flange Type Check Valve
TC4
Because the check valve flange type doesn’t tapping on the flange hole, installation of double...
Details