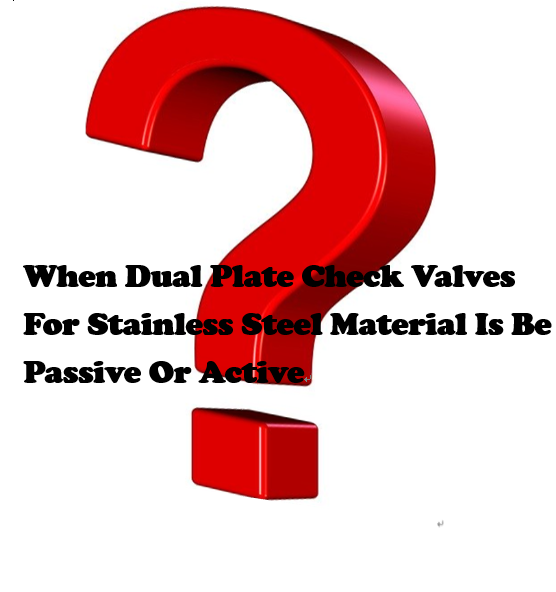
Q.When Dual Plate Check Valves For Stainless Steel Material Is Be Passive Or Active - Formation Of The Passive Layer
The inherent corrosion resistance of stainless steels is derived from alloying the base iron with chromium. BS EN 10088-1 states that a steel must have a minimum of 10.5% (by weight) chromium and a maximum of 1.2% carbon to be classified as 'stainless'.
Other alloying elements including nickel, molybdenum, nitrogen, titanium (or niobium) are added to form the various grades. These additions are made to enhance the 'basic' corrosion resistance of the steel but can also usefully modify other properties, such as formability, strength and cryogenic toughness.
The corrosion resistance of stainless steel arises from a 'passive', chromium-rich, oxide film that forms naturally on the surface of the steel. Although extremely thin at 1-5 nanometres (i.e. 1-5 x 10-9 metres) thick, this protective film is strongly adherent, and chemically stable (i.e. passive) under conditions which provide sufficient oxygen to the surface. This 'normal' condition is the passive state.
The key to the durability of the corrosion resistance of stainless steels is that if the film is damaged it will normally self repair (provided there is sufficient oxygen available). However, under certain conditions, the passive state can be broken down, resulting in corrosive attack.If damaged, the film will normally repair itself. If the film is destroyed the surface is said to be in the active state.
- Related Products
Dual Plate Wafer Type Check Valve
TC0
Fast Delivery: Most orders are shipped within 3-7 days, depending on stock availability. Versatile...
DetailsDual Plate Wafer Type Check Valve With Retainerless
TC8
The dual disc check valve with its compact wafer design and low cost have made it a popular...
DetailsDual Plate Flange Type Check Valve
TC4
Because the check valve flange type doesn’t tapping on the flange hole, installation of double...
Details